

One step ahead
What unites top-level specialists of any industry? High earnings and demand? I think no. It is rather the result of their hard work. And it unites them - an incredibly great desire to learn and develop, and the latest software or tool developments. How can a young, talented racer achieve high prizes without a modern race car? Or will a young, brilliant surgeon doctor reveal his talent without an experienced mentor and innovative developments in medical equipment? So an engineer - a technologist will never be super unless he keeps up with the times.
Today, an increasing number of machine-building enterprises is re-equipping their equipment fleet. But how many turning axes a CNC machine would not have, anyway, it's just a set of mechanisms that need to be properly controlled. First of all, we are talking about control programs (UP) for CNC machines. Methods for obtaining control programs can be different - from writing manually (last century) to using CAM-systems. Work manually or using simple systems inside the CNC machine
It is accompanied by many difficulties - here is a long time for writing programs, and significant restrictions on the possibility of processing parts, lack of security checks, etc. As for CAM-systems, I’ll say the following: there are quite a lot of such systems in the world in terms of capabilities, prices, and so-called “levels,” but there are few peers to solve complex problems in terms of preparing control programs, such as ease of development and incredible capabilities CAM systems like FeatureCAM and PowerMILL.
FeatureCAM. This software product is designed to develop effective control programs for turning, milling, turning and milling processing and wire EDM cutting. Its main distinguishing feature is the extremely high degree of automation in the development of reliable control programs that ensure a consistently high quality of processing on modern multi-axis CNC machines.
PowerMILL is the world's leading CAM system for the treatment of surfaces of complex shapes found in the aerospace, gas, chemical, automotive and machine tool industries and in the manufacture of medical equipment. An important advantage of PowerMILL is that a wide range of cutting tools can be used for 5-axis toolpaths, including end, ball and rounded, disk, conical, conical spherical and conical rounded mills. As a rule, other systems are limited to using only ball and end mills, which is not always effective, especially at the roughing stage.
Conducting a conversation about leading CAM systems, one cannot help but touch upon the subject of postprocessors. A postprocessor is an optional file that contains information about the configuration of the equipment and the CNC system installed on this equipment. This is an incredibly important part when writing programs for CNC machines.
When developing a postprocessor, we are dealing with two fundamental objects of CAM systems: The trajectory is the curve of the movement of the edge of the center of the tool, which the software engineer calculates in the CAM system. The trajectory consists of linear sections and arcs. The path data set is called CLDATA. Such information is not understandable for the machine, but with the help of a post-processor specially designed for a specific CNC system and obtaining a control program, the machine performs all the necessary actions and correctly performs the workpiece processing.
A control program is a set of data in a given format (in the language of a specific CNC) for controlling the movement of the working bodies of the machine, as well as other devices installed on it. An ideally written post-processor allows you to completely eliminate the “manual” intervention of a technologist or CNC operator in the program, which is a guarantee of safe operation, and also significantly reduce the development of technological processes.


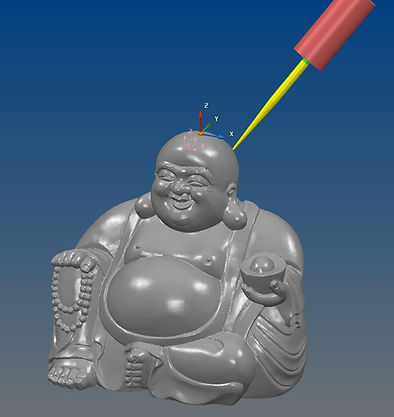
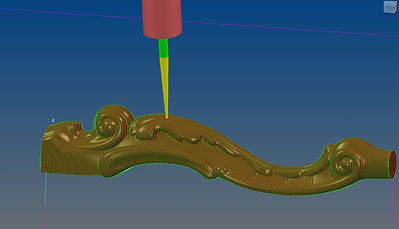
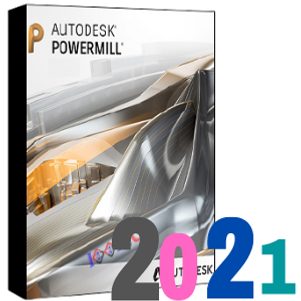